|
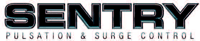
Blacoh Sentry Suction Stabilizers
Protect Inlet System Components
Positive displacement (PD) pumps contain an inlet valve that alternately opens and closes, creating an acceleration and deceleration of fluid into the pump. Depending on process fluid characteristics and pipe arrangement, there will either be a scarcity or abundance of pressure and/or flow at the pump's inlet. The "J" Model Inlet Stabilizer effectively works to minimize these pressure fluctuations and acceleration head losses by preventing fluid column separation at the pump's inlet.
The "J" Model's control unit consists of a compound pressure gauge, a vacuum tight ball valve, and a venturi valve. Compressed air passed through the venturi valve at high speed creates a low pressure area. This evacuates air from the stabilizer and creates an internal vacuum. Conversely, when the flow of air through the venturi valve is diverted into the stabilizer, a pressure charge is obtained, optimizing pump efficiency and productivity.
|
|
|
Use an Inlet Stabilizer To:
- Ensure complete chamber fill, extending component service life.
- Protect pumps, valves, diaphragms, and pistons from excess stress and strain.
- Protect inlet components from vibration and fatigue.
- Ensure accuracy of inlet side gauges.
- Prevent premature system component failure.
- Prevent cavitation.
- Prevent gauge damage due to vibration.
- Extend diaphragm life in all diaphragm pumps.
"J" Model Features:
- Improved inlet flow conditions.
- Patented control unit allows you to adjust for pressure or vacuum settings.
- Regulates for suction lift or positive inlet pump conditions.
- Available in 10 cu in (.16L) to 10 gallon (37.85L) sizes.
- All standard models available from stock.
- Bodies available in a full range of chemically resistant materials.
|
Case – High Inlet Pressure (Positive Inlet) |
Under high inlet pressure, liquid flow is abruptly stopped as the inlet valve closes. This rapid deceleration creates a pressure spike or "water hammer," with pressures increased by a factor up to five. With higher differential pressures in which inlet valves close even faster, these pressure spikes are further increased. Constant repetition puts significant strain on the system, and may result in system fatigue or failure.
Air-operated diaphragm pumps are particularly susceptible to this phenomenon. As one AODD inlet valve closes, the inlet valve in the opposite chamber opens. The resultant pressure spike travels into the liquid chamber and slams against the diaphragm, stretching and weakening this crucial component. The "J" Model Inlet Stabilizer effectively cushions and absorbs such pressure spikes, increasing overall system life and productivity. |
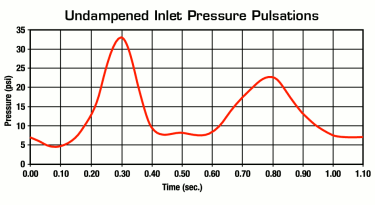 |
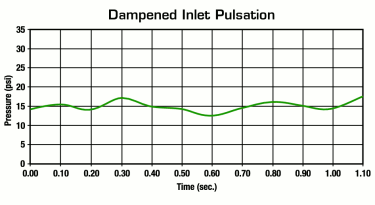 |
Case – Low Inlet Pressure (Suction Lift) |
Under low inlet pressure, process fluid separates at the pump's inlet as the inlet valve closes. Depending on system design, low inlet pressure (NPSH available) may not be enough to meet required inlet pressure (NPSH required). For example, undersized pipes or pipes too lengthy for the viscosity or vapor pressure of the liquid can result in product starvation or "cavitation." Cavitation occurs when pressure in the pump's inlet drops below the vapor pressure of the liquid being pumped. This causes severe damage to the pump's suction end components, severe pitting on pistons and plungers, and drastically reduces diaphragm life.
Multiple head pumps are particularly predisposed to fluid starvation, as each fluid chamber pulls product through inlet runners of unequal lengths. The "J" Model Inlet Stabilizer effectively reduces liquid starvation and cavitation by acting as a storage accumulator. As such, when the inlet valve opens on the discharge stroke, the "J" Model puts fluid back into the line, maintaining inlet pressure and constant flow. |
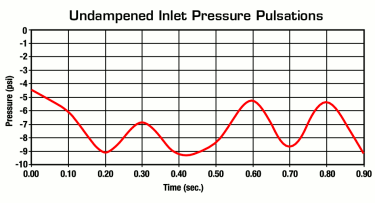 |
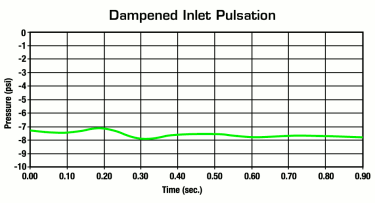 |
|
|
Hours of Operation:
Monday – Friday, 8:30 a.m. – 5 p.m. EST
|
| |