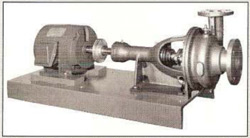
Photo 1: Industrial frame mounted unit used for early CIP service – circa 1957.
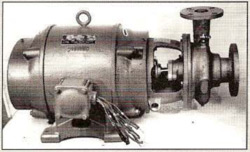
Photo 2: Typical close-coupled centrifugal design used for CIP applications in the late 1950s and early 1960s.
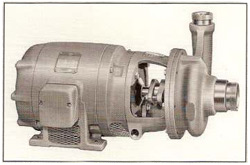
Photo 3: A major 1960 modification eliminated the pump's suction and discharge flanges from the casing.
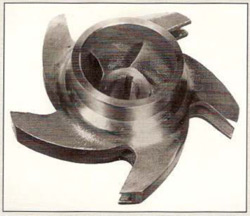
Photo 4: The Hydro-Dyne impeller introduced in 1966 altered the traditional configuration of fully shrouded impellers.
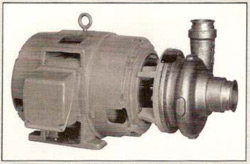
Photo 5: The 1970 Type JM close-coupled pump motor reduced shaft overhang.
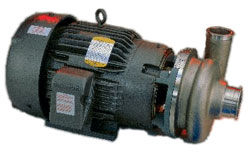
Photo 6: Ampco introduced the
D Series pump line manufactured exclusively for CIP operation in 1988.
Ampco Pumps' first venture into CIP service occurred in 1957 when a standard industrial frame mounted 2½" x 2" unit was purchased by a Wisconsin dairy to pump 150 gpm at a head of 90 feet (Photo 1). This pump replaced a cast iron unit that was leaking badly through the stuffing box area and had a severely corroded housing. The wetted end of the replacement pump was 316 stainless steel (CF-8M), with a mechanical seal like those used in the chemical processing industries.
Because the service is relatively mild compared to the standards required for equipment in the chemical processing industry, pumps intended for CIP applications were ususally economical, compact, close-coupled designs (Photo 2). In such a configuration, the pump is mounted integrally on the motor rather than using a frame-mounted base design in which the pedestal relieves the motor of bearing loads, pump shaft leakage and heat – all important considerations in chemical processing.
The close coupled pump motor became popular almost immediately because it was more compact and economical. Shaft sealing (both packed stuffing boxes and bellow style mechanical seals) were utilized in early designs, but leakage often resulted in premature failure of the motor's inboard bearing. Furthermore, attempts to reduce leakage by installing mechanical seals were hampered primarily by the lack of a satisfactory seal material. Standard ceramic, ni-resist and tungsten carbide had all been corrosively attacked on the seal mating surfaces by various cleaning agents. Work with a major seal manufacturer and experience with several Midwest field installations resulted in the development of a new seal material (High Purity Ceramic by Coors), which remains a standard today. In cases where thermal shock may occur (due to an abrupt liquid temperature differential of 100°F or more), hard faced stainless steel seats now provide a reasonable alternative.
In the early years of clean-in-place systems, totally enclosed fan cooled (TEFC) motors were inadequate for dairy service because they developed condensation in humid environments, and the one-way condensation drain holes found in today's designs weren't available in the 1960s. The popular motor that emerged was the open drip proof enclosure type with encapsulated windings and an oil seal arrangement in the motor housing that protected the inboard bearing.
Current close-coupled pump motor selection provides several options relative to enclosures, including TEFC and both rolled steel and cast iron construction, epoxy finished rolled steel TEFC with "double sealed" bearings, and an all stainless rolled steel TEFC motor with a contact lip seal on shaft extensions and special process cast end plates.
A major 1960 modification eliminated the pump's suction and discharge flanges from the casing (Photo 3). This reduced the component weight by 25%. Replacing the flanges were ferrules with sanitary connections for both inlet and outlet. Since there were at least 18 different designs of sanitary connections available at the time, customers could select the desired connections and have them brazed into the pump housing.
To effect further cost reduction goals, Ampco introduced a patented "Hydro-Dyne" impeller (Photo 4) in 1966. This altered the traditional configuration of fully shrouded impellers and eliminated the need for hydraulic balancing chambers. It also enabled entrapment areas to be removed, vane and casing reduced and flow guidance improved.
In 1969 a Type JM close-coupled pump motor ("T" Series), developed jointly by the Hydraulic Institute and NEMA (National Electrical Manufacturers Association), featured a more compact and economical design that reduced shaft overhang (Photo 5). This modification resulted in longer motor bearing life because of reduced bearing loads, a decrease in motor shaft deflection, and higher life expectancy for the mechanical seal sue to reduced opening between the seal faces on each revolution – making it harder for sediment, dirt or other particles to enter.
During the same era the 3-A CIP accepted practices for permanently installed sanitary product lines and cleaning systems (Specifications 605-O2) called for an SIS #3 cast finish (green sand molding - 500 RMS) as the minimum requirement.
Throughout the 1980s seven draft proposals were submitted relative to 3-A CIP practices, primarily concerning pumps. Major changes included a new cast surface finish requirement (200 RMS), elimination of exposed threaded connections (NPT or UNS standards) and counter-bore depth limitations.
To remain abreast of proposed 3-A practices, Ampco proceeded to retool and eventually introduced a new pump line – the D Series – manufactured exclusively for CIP operation (Photo 6). The current version of this pump is in conformance with 3-A Standard number 47-00 which became effective in November 1996 and established a standard specifically for CIP dairy applications complete with a sanitary seal.
John H. Horwath is a Senior Technical Consultant with Ampco Pumps Company in Milwaukee, WI.